The numerical control (NC) machine tool with parallel tool head as the core part is an important supplement to the traditional serial machine tool, which satisfies the requirements of high accuracy and high efficiency in aviation industry and has been proved to be an effective method to solve the aviation machining problem. However, as a complex mechatronic equipment, developing parallel tool head with good motion performance is a challenge. At present, China is still in the stage of key technology development.
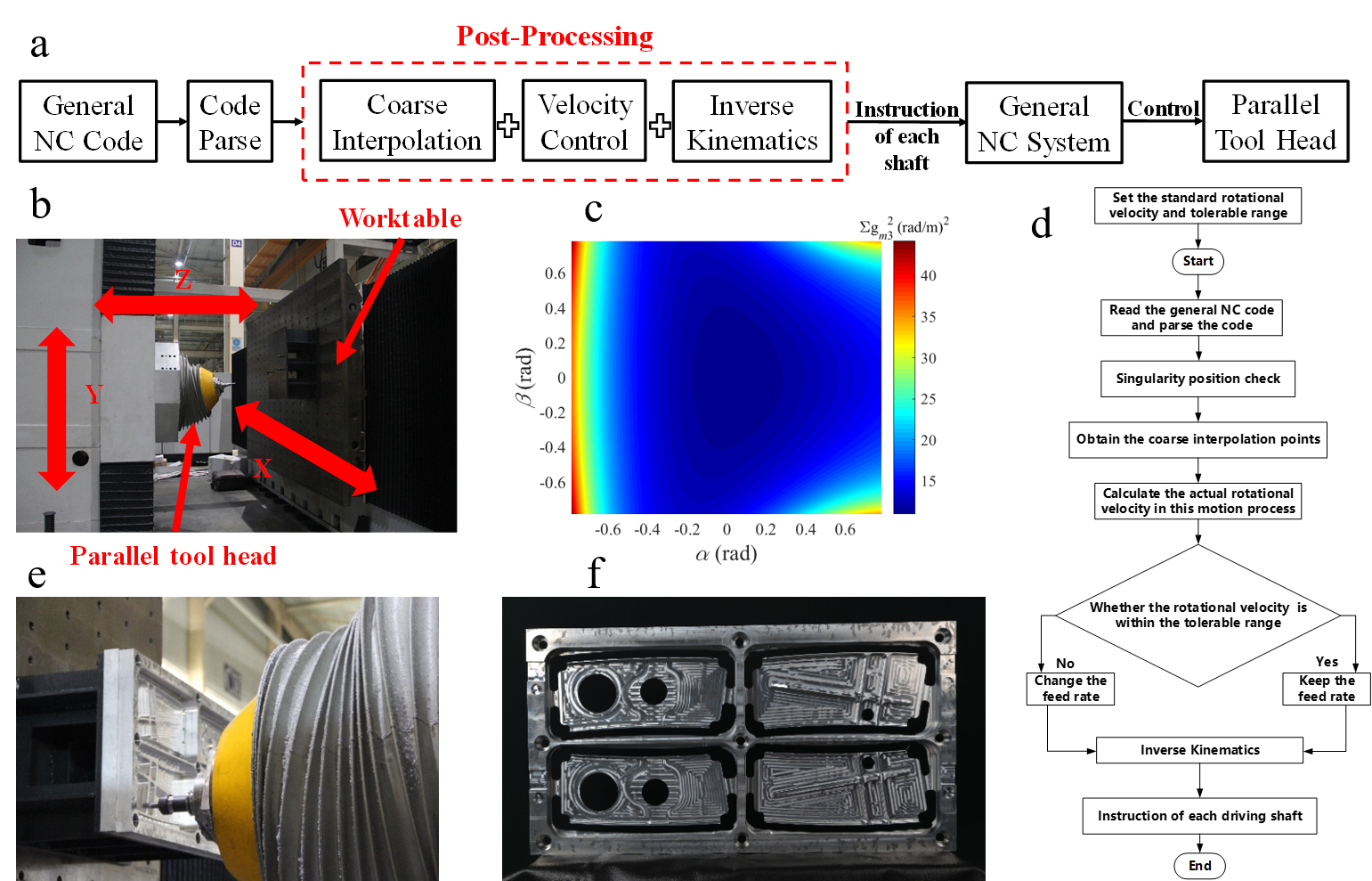
(a) The postprocessing flow of the parallel tool head; (b) The prototype of the spatial parallel tool head; (c) The evaluation of the velocity transfer characteristic; (d) The feed rate optimization flow; (e) The cutting experiment; (f) The finished aircraft structural parts with thin walls.
Due to the coupling structure characteristic with multi closed-loop chains of the parallel tool head, there would exist obvious rotational velocity fluctuation in task space, which heavily affects the motion stability and decreases the machining quality. In order to solve this problem, the research group has carried out a series of work. First, a velocity transfer model of the parallel tool head from joint space to task space is established, and the time-varying and coupling velocity transfer characteristics are further evaluated. Then, a rotational velocity control method is proposed by optimizing the feed rate, which could efficiently solve the rotational velocity fluctuation problem. Finally, the method is integrated to the postprocessing process to ensure the motion stability of the parallel tool head in any trajectories.
The research result has been published in the journal IEEE Transactions on Industrial Electronics (2018, 2018, 65(8): 6333-6342), as the title of “A postprocessing strategy of a 3-DOF parallel tool head based on velocity control and coarse interpolation”, and the Ph.D student Dong Wang is the first author. This research is supported by the National Natural Science Foundation of China under Grant 51622505 and Grant 51575307, and the Science and Technology Major Project-Advanced NC Machine Tools and Basic Manufacturing Equipments under Grant 2016ZX04004004. In recent years, a series of research achievements about parallel mechanism and its application have been made by the research group of Prof. Jun Wu and Prof. Liping Wang, which have been published in IEEE/ASME Transactions on Mechatronics (2016, 21(1): 88-97), Mechatronics (2017, 2017, 41: 102-113) and Mechanism and Machine Theory (2018, 121: 430-445).
The article link: https://ieeexplore.ieee.org/abstract/document/8219752