Line contacts are widely used in the mechanical engineering, such as roller bearing, gears, cams and cylinder line-piston ring friction pair. Running-in process is very common for a new machine or component after the start of sliding between contacting surfaces. Wear profile and surface roughness of initial line contacts are continuously varying with sliding distance until lubrication contact system eventually comes to a steady-state.
This paper studied the running-in process of initial line contacts under mixed lubrication. A numerical approach was developed on the basis of stochastic solution of mixed lubrication. Sugimura’s wear model was modified and used to link the wear particle size distribution and the variation of surface height PDF during wear. The wear depth on the contact region was estimated according to the modified Archard’s wear model using asperity contact pressure. The simulation results showed that the lubrication condition in which small wear particles are generated from the asperity contact region is beneficial to reduce friction coefficient andwear rate, and leads to a better steady mixed lubrication condition.
This paper is published on the ASME Journal of Tribology in May, 2018.
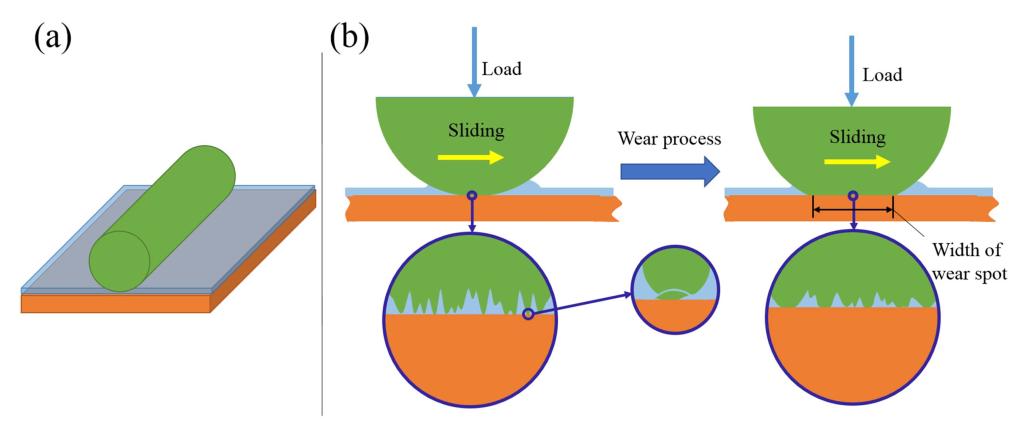
Fig. 1 Wear process of initial line contact at mixed lubrication regime.
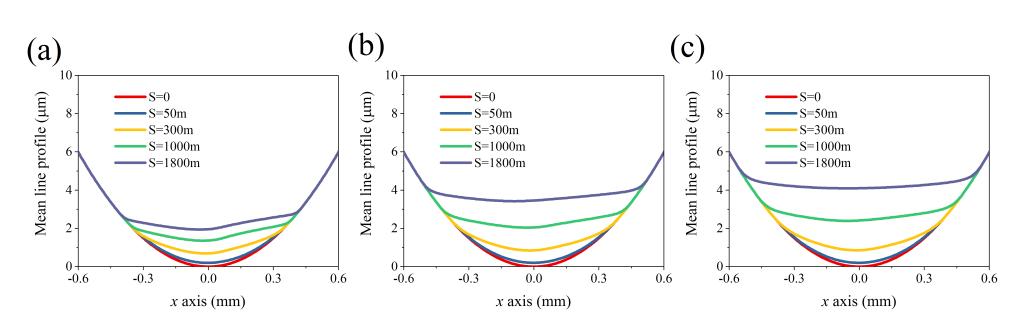
Fig. 2 Variation of cylinder profile during the wear process with different lubrication conditions.
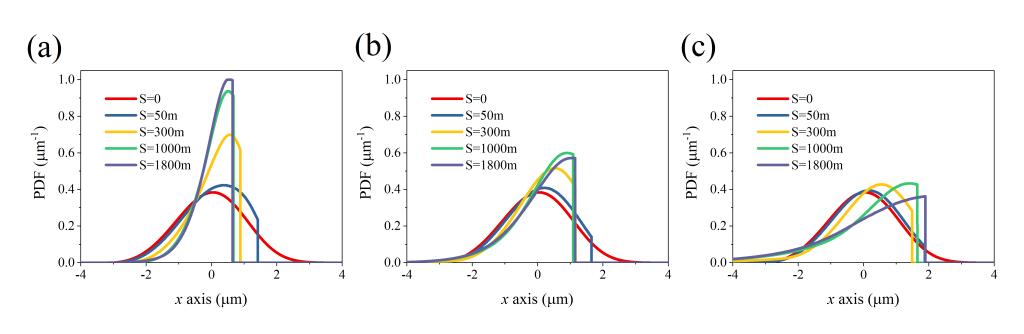
Fig. 3 Changes of height probability density function during the lubrication process.
The original link: http://tribology.asmedigitalcollection.asme.org/article.aspx?articleid=2678180